What motivates development engineer, Guy Blanch, is turning ideas into practical action to solve problems, and that is exactly what he has been doing for the last 20 years.
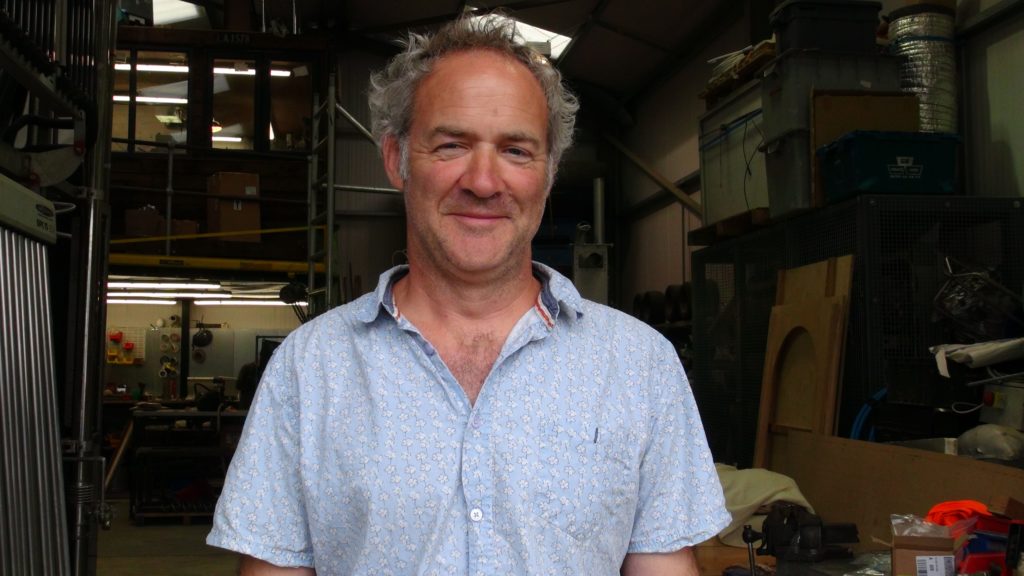
Since graduating with a degree in engineering, 47-year-old Guy, from Wiltshire in the UK, has worked on a wide variety of research and development projects – from working with schools to educate children on composting and food waste reduction, to engineering innovative mobile units to help farmers reduce waste and process fruit juice in developing countries like Uganda and Nigeria.
All his projects have something in common – finding practical solutions to problems that benefit the environment, agriculture, or communities, or all three.
Based on the site of the business his grandfather started more than 60 years ago, his workshop near Malmesbury in the South West of England is a hive of activity. In his onsite office, you can hear intermittent power tool and hammering sounds as work continues in the main workshop. It was while managing development projects for the family business – Alvan Blanch Development Company – in 2014, that he developed a mobile fruit processing unit for Makerere University in Kampala, Uganda. The aim of the unit? To encourage business and marketing experience for post graduate students and to reduce post-harvest costs and food waste.
“One of the projects I did for Alvan Blanch was a mobile fruit juicing project and that’s what kind of got me interested in the whole mobile thing,” says Guy. “The idea is that the truck is used to process fruit out in the field, saving the farmer from travelling into the local market and the fruit piling up and it all being wasted”
“There are different seasons for the fruits – like water-melons, guava and mangoes – and the truck can utilise those seasons, it can make the most of the time when the fruits are ripe and turn them into juice. It also means the waste by-products – the seeds, the stones and the skins – can all go back to the land and are not travelling lots of miles.”
Water is the key for mobile processing
But there are many challenges associated with producing mobile units, as Guy explains: “Water is really the key for this kind of mobile processing, so we had to add a water purification filtration system and on-board storage.”
“The juice is obviously very sticky and you’ve got lots of flies around, so you need to be able to wash it all off at the end of a shift and clean it down and it needs to be safe. Because of the high ambient temperatures, bacteria will breed fast, so wash down water is imperative to the process to succeed.”
“We also had to have a pasteuriser on board so that once you’ve separated the juice from the fruit you can ensure the juice is safe for longer term storage.”
After developing the plans and building the system over 11 months for Makerere University at the Alvan Blanch factory, Guy spent three weeks in Uganda commissioning the project and the truck, supplied by the University, and training operators in how to use it effectively.
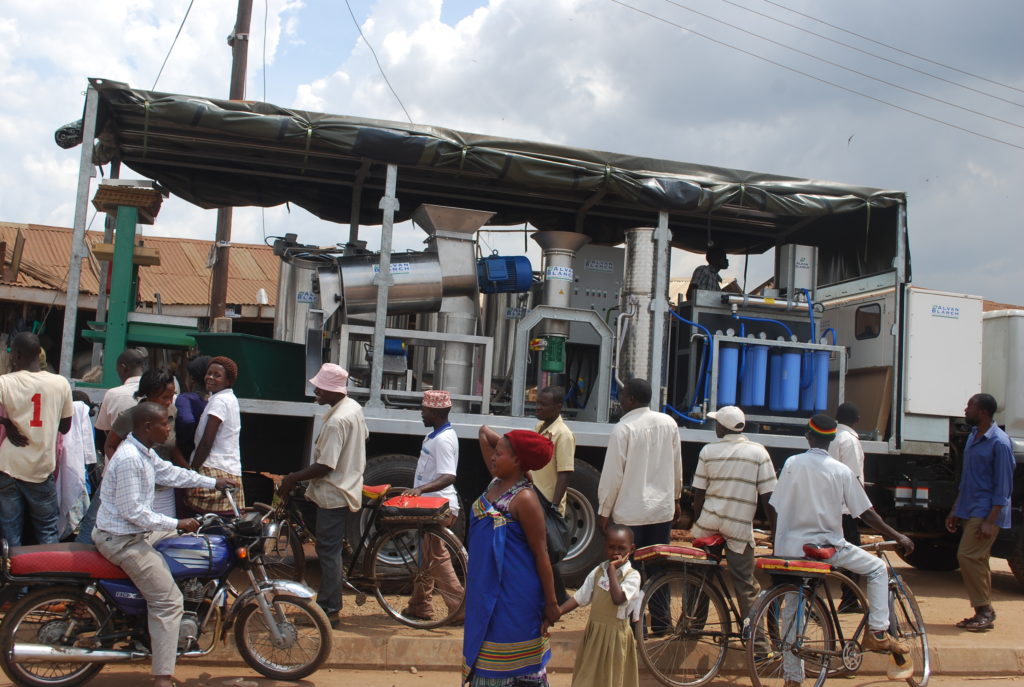
In 2014, this project attracted a lot of attention, not only from the farmers and members of the public, but from a national Ugandan TV news station, which broadcast the project’s story. However, Guy is modest about the reaction to the broadcast.
“It was quite fun and it did cause quite a stir when we arrived with people asking why are you here and why are you doing this, but I think the biggest reaction was at the end of a shift when we were handing out fresh pineapple juice!”
The challenges of decontaminating human and animal waste
It was while working on a sanitation project in Madagascar that Guy really became engaged with pasteurisation and the challenges associated with decontaminating human waste. The project helped reinforce the vital importance of water use and storage for these projects as well as the need to make sure the process is energy efficient.
“It involved developing a multi-fuel pasteuriser for processing human waste,” says Guy, “but it soon became apparent that despite the fact we had sterilised a considerable batch of waste and made it relatively safe in biological terms, our carbon footprint for fuelling that process was massive!”
“Unfortunately, both human and animal waste are contaminated with a cocktail of drugs and anti-biotics, which have potentially disastrous long-term impacts for our soils, unless we can develop more effective solutions, coupled with changes to legislation surrounding biomass waste.”
Elevating an idea to a ready- to-use mobile application
The combination of Guy’s experience and that of his company LEAP – formed with business partner Rokiah Yaman – makes them ideal partners in the 3-year EU-funded NOMAD Project to find a cost-effective and mobile solution to creating earth-kind bio-fertilisers. LEAP’s role is to lead the design, build and testing of the mobile technology as well as coordinating operator training and technical support for the trials in each of the demonstration countries – the UK, Malta, Italy and Greece.
“The solid or liquid fertilisers commonly used today by farmers to support crop growth, is ‘digestate’ produced by anaerobic digestion (AD) and do contain valuable nutrients and fibre,” says Guy. “However, digestate’s long-term use can have negative impacts on soil, such as decreased worm populations and acidification.”
“Processing this digestate to avoid these harmful long-term impacts is currently not really an option for small scale farmers due to a lack of available, cost-effective equipment. With climate, waste, energy, and circular economy policies all driving growth of the AD sector worldwide, there is now an urgent need to address the lack of a mobile solution to address this major issue and that’s what NOMAD aims to achieve.”
Led by CERTH (The Centre for Research & Technology Hellas) in Greece, NOMAD has 14 other partners from the UK, Macedonia, the Netherlands, Romania, Malta, Italy, China and Germany, bringing together knowledge and skills in engineering, technology, water processing, research, engagement and communications.
Transforming slurry into usable grey water
Currently in the design stage, the aim is to have a mobile unit ready for trial in early 2021 – corona virus pandemic delays permitting. Before that can be achieved, the team has a number of challenges to overcome including decontaminating the waste that’s used, producing a grey water from the digestate that can be used elsewhere on farm, taking into account relevant EU environmental legislation, as well as making sure the end product is cost-effective.
“There are many current unknowns in this project and that’s what makes it so interesting,” says Guy. The engineering is a relatively small part but the biology behind it is really rather interesting. The antibiotic materials that are coming from human and animal waste streams are left in the slurry and can then potentially be transferred to the soil, so we need to decontaminate it.”
“The food waste provides a different challenge as it contains a lot of microplastics which, again, are a contamination concern. And then there’s water, which is very important, as once the nutrients have been extracted we want to be able to provide a ‘grey’ or waste water that can be used for irrigation or for washing out glasshouses, for example.“
Developing a sustainable and cost-effective solution is key
Politics and legislation will also be under consideration as a core part of this project. Guy and the NOMAD team are looking at ways to prevent chemicals like chlorine and by-products including heavy metals, microplastics and other pollutants, ending up in our waste and, ultimately, in our soils.
“Legislation varies across Europe with regard to fertilising crops and, if the deal goes ahead with the US, we may see feedstocks coming into the farms or from slaughterhouses to AD sites which potentially contain a variety of contaminants that we don’t really know about, and for which they will have to be tested.”
“Another challenge is that we really have to try and keep it a cost-effective solution. Fertiliser costs in Africa are much higher than in Europe so being able to offer a cost-effective solution down the line for developing nations is a key ambition for us.”
Despite his extensive experience of development engineering projects over 20 years, the NOMAD project is Guy’s first experience of partnering in an EU-funded project.
“One of things I’ve enjoyed is working with universities. In many ways, we’re chalk and cheese – you have academics with access to amazing theoretical resources and detailed research, and then there’s the more practical and commercial side. Turning ideas into actual products, that’s the fun bit for me, the in-depth research that goes with it – not so much – but being able to access and work with researchers who really understand their business, that’s really exciting.”
In the spirit of a true development engineer, Guy is already thinking about solutions he wants to develop in future projects arising from NOMAD. When explaining about potential uses for water produced from waste, he says:
“It would be really nice to get that grey water into a potable water because if you can recover the nutrients from waste and then (eventually) provide drinking water, you’re really onto something, but that’s still quite a few steps down the line. Perhaps for a future project.”
Special thanks to Charlotte Reid (Minerva Communications UK Ltd).